Sergio Castro, Gerente General – Castro Ingeniería
Introducción
Los yacimientos de Cu porfídicos contienen Mo como sub-producto, con leyes entre 100 y 600 ppm.
Para que el Mo llegue a un producto comercial, se debe procesar hasta un concentrado de molibdenita (MoS2), con leyes de Mo entre 48 y 52%. El proceso global se realiza en 2 etapas: (1) Flotación colectiva Cu-Mo (planta concentradora), donde se obtiene un concentrado bulk Cu-Mo, con leyes entre 0.2 y 0.8% Mo); y (2) Flotación selectiva de Mo (planta de moly), donde se produce el concentrado final de molibdenita.
Flotación selectiva de Mo
Esta nota técnica se centrará solo en la planta de molibdeno. Al igual que el azufre, el talco, y el grafito, la molibdenita exhibe hidrofobicidad intrínseca. Esta propiedad determina su flotabilidad natural, aspecto clave en la separación Cu/Mo. Gracias a ella, la molibdenita flota cuando los sulfuros de Cu y Fe son depresados por sulfhidrato de sodio (NaHS), haciendo técnicamente factible la separación selectiva Cu/Mo.
Dado que el NaHS es un agente reductor y un alcalinizante, las variables más relevantes del proceso son el potencial ORP (medido entre un electrodo de Pt y un electrodo de Ag/AgCl); y el pH de la pulpa.
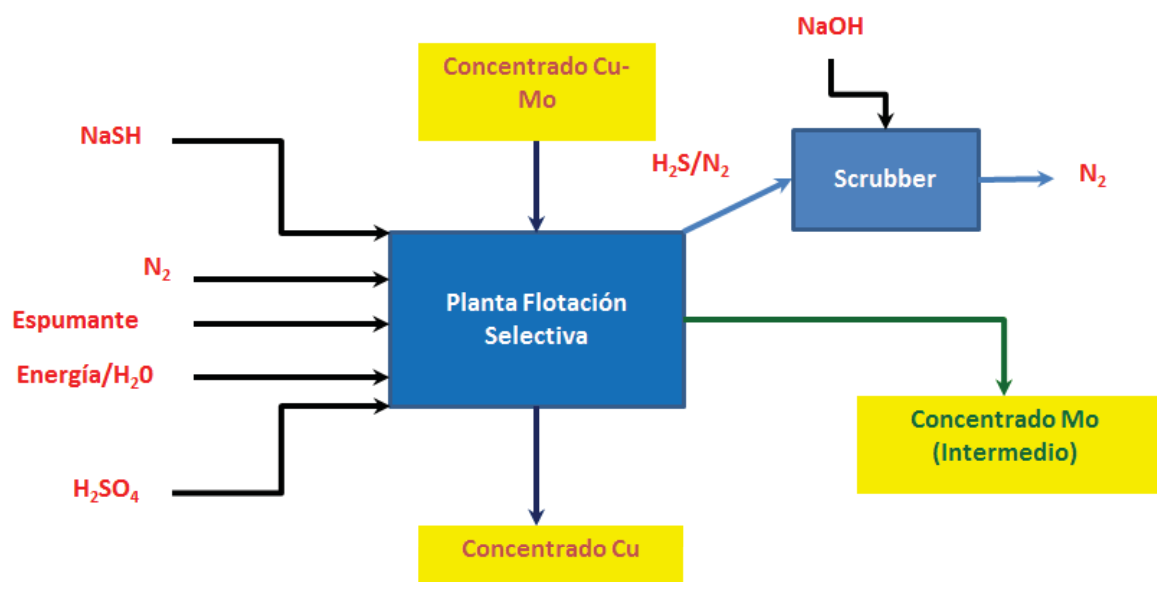
Figura 1. Representación esquemática de una planta de moly.
La flotabilidad natural de la molibdenita se debe a su estructura cristalina laminar. El cristal es de forma hexagonal, y su plano basal es hidrófobo debido a que está cubierto por átomos de azufre. En cambio, los bordes del cristal son hidrofílicos, porque exponen los enlaces covalentes S-Mo-S que interactúan con agua formando iones molibdato. Así, la hidrofobicidad de una partícula de molibdenita depende de su tamaño y de la razón bordes/caras. Las partículas finas son menos hidrofóbicas pues tienen una mayor razón bordes/caras.
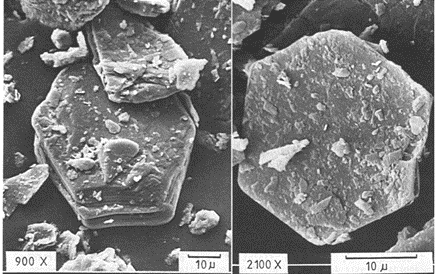
Figura 2. Microfotografía de cristales laminares hexagonales de molibdenita.
Golpe de ácido sulfúrico
La planta de moly se alimenta con la descarga del espesador de concentrado colectivo Cu-Mo (proveniente de la concentradora). Esta descarga, primero pasa por un estanque donde se adiciona ácido sulfúrico, para bajar el pH hasta un valor entre 7.5 y 8.5, dependiendo de si se dispone o no de un adecuado sistema de manejo del gas H2S. El objetivo de esta etapa es lograr una limpieza química de la superficie de las partículas de molibdenita, eliminando el Ca residual resultante de la depresión de pirita con cal en la planta concentradora.
NaHS y control de potencial ORP
El depresante de Cu más utilizado en las plantas de Mo es el NaHS. El ion sulfhidrato (HS–) actúa como un efectivo depresor de los sulfuros de Cu y Fe (calcosina: Cu2S; calcopirita: CuFeS2; pirita: FeS2; etc.). Su acción se explica porque el ion HS– destruye el recubrimiento de colector sobre las partículas sulfuradas de Cu y Fe. La desorción del colector es responsable de la pérdida de su flotabilidad. Sin embargo, esta desorción es temporal y exige que se mantenga una cierta concentración residual crítica de NaHS, de lo contrario, el colector se re-adsorbe y los sulfuros de Cu vuelven a flotar.
Para asegurar esta concentración crítica de NaHS, se debe mantener un potencial ORP entre -500 y -600 mV, medido en la última celda o en la descarga de cada circuito.
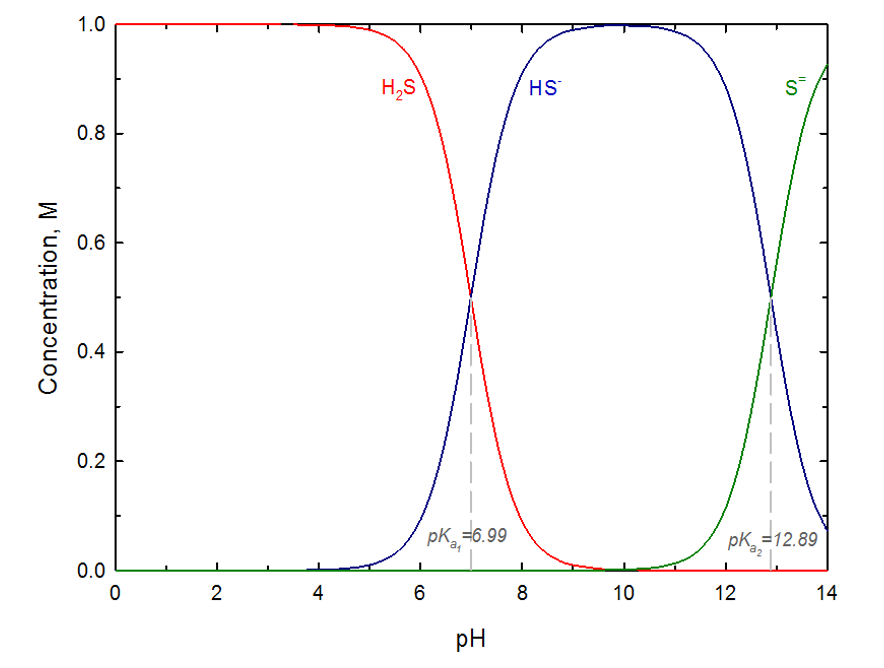
Figura 3. Diagrama de hidrólisis del ácido sulfhídrico (H2S).
Cabe hacer notar, que el potencial ORP de una pulpa depende del pH de flotación. Una misma concentración de ion HS–, puede tener distintos valores ORP, según sea el pH. Por ejemplo, si el potencial de una solución de NaHS fuera -440mV a pH 8, y se sube a pH 9, el ORP debiera cambiar a un valor alrededor de -510 mV (ver Figura 4). Existe una relación lineal de pendiente negativa entre el potencial ORP y el pH (baja alrededor de -60 mV al aumentar el pH en una unidad, lo cual se explica por la ecuación de Nernst). En la práctica la pendiente varía levemente entre una planta y otra.
Para efectos de control del proceso, el potencial ORP medido en la planta debiera manejarse en la línea roja (Figura 4). En cambio, si los valores experimentales caen por encima, es indicación de que la depresión de Cu es insuficiente; y si caen por debajo, se estaría usando un exceso de NaHS.
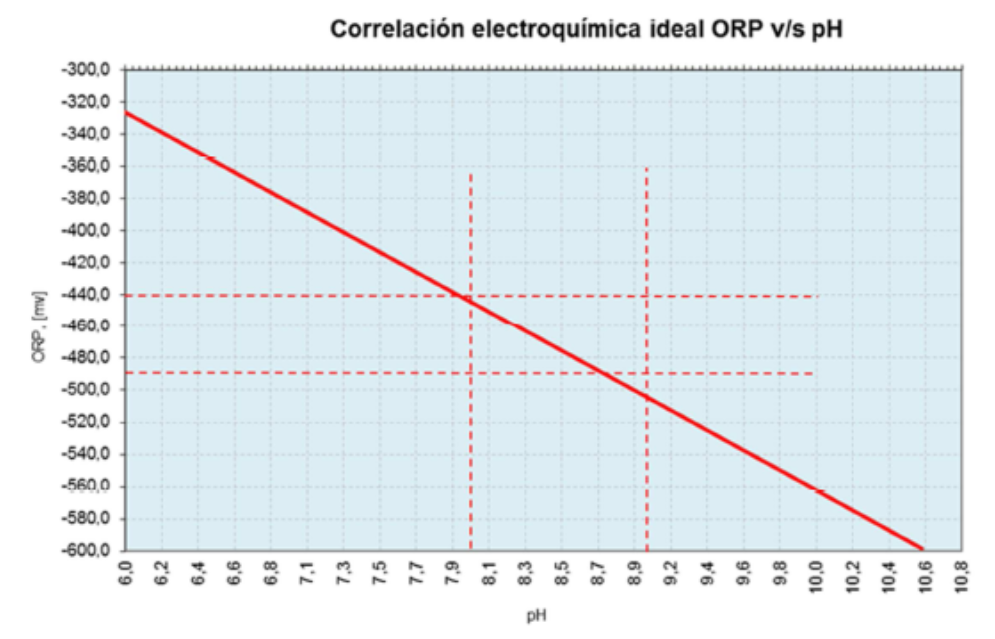
Figura 4. Correlación entre potencial ORP y pH en una pulpa con NaHS.
Estabilidad química del NaHS
El NaHS representa el mayor costo de operación de una planta de molibdeno. Además, es un fuerte agente reductor, por lo cual tiene tendencia a oxidarse. Es inestable en un ambiente con oxígeno, especialmente en un sistema particulado, como lo son las pulpas de concentrados. Los productos de oxidación son tiosulfato (S2O32-) y sulfito (SO32-). Sin embargo, el tiosulfato y sulfito carecen de acción depresora sobre el Cu, por lo cual la oxidación del ion HS– es una reacción lateral no deseada.
El NaHS también hidroliza con el pH. A pH 7 el 50% se encuentra como H2S y el otro 50% como ion HS– (Figura 2). Hay que considerar que a pH<9.0 ya se forma una pequeña fracción de H2S, y se incrementará a medida que bajamos el pH.
El H2S tiene baja solubilidad en agua, por lo cual, una vez alcanzada la saturación, el exceso de H2S gas se desprende a la atmósfera, y como gas es altamente tóxico y pestilente. Para prevenir esta situación se debe disponer de un sistema de lavado de gases (scrubber) (neutralización de los gases con solución de NaOH), especialmente cuando la flotación se opera a pH bajo, p.ej., entre pH 7.5 y 8.5.
Tipos de celdas en flotación de moly
Se han desarrollado celdas especiales para operar plantas de moly, que buscan minimizar la oxidación del NaHS, y a la vez operar a pH bajo. Estas son celdas convencionales cerradas (herméticas, auto-aspirantes), con recirculación interna del aire, lo cual, consume el oxígeno dando lugar a aire enrarecido (similar a un gas inerte). En cambio, si la celda es abierta, lo anterior es inaplicable y se recomienda reemplazar el aire de la flotación por nitrógeno. Esto se aplica en plantas de moly cercanas a fundiciones que disponen de plantas de oxígeno (las cuales producen nitrógeno como sub-producto).
Respecto al diseño de la planta de moly, el circuito rougher y los circuitos de limpiezas, usualmente, se diseñan con celdas convencionales cerradas y herméticas (celdas de 2000; 1000 y 500 pie3). La última etapa de limpieza se diseña con celdas en columna.
Efecto de las cargas circulantes
Las plantas de moly consideran varias etapas de limpiezas (entre 3 y 6), por lo cual durante su operación se pueden generar grandes cargas circulantes, debido a que por diseño las colas recirculan en contracorriente.
Las partículas finas de gangas y de molibdenita en cada circuito tienden a irse por las colas, y finalmente terminan formando parte de la cola de primera limpieza. Por diseño, lo usual es que esta cola se mezcle con la alimentación fresca, para formar la alimentación compuesta. Sin embargo, la alimentación fresca tiene buena flotabilidad, mientras que la cola de primera limpieza presenta problemas de recuperación, espumación y arrastre físico de lamas. En muchos casos, la alimentación fresca se desestabiliza con el aumento de caudal de la cola de primera limpieza, produciendo una fuerte caída en la recuperación de Mo del circuito rougher. Se recomienda evitar que aumente la carga circulante de las colas en contracorriente.
Problemas frecuentes en plantas de moly
Además del anterior, son numerosos los problemas que pueden afectar el desempeño metalúrgico de una planta de moly. El circuito rougher es clave, y se recomienda operarlo lo más estable y selectivo que sea posible.
Las plantas de moly son en realidad plantas de depresión de Cu, pues prácticamente no se hace nada para que la moly flote, salvo agregar algo de diésel oil y espumante.
Exige un adecuado control del potencial ORP, cuyo valor dependerá del pH de trabajo. Se recomienda aplicar un control simultáneo y sincronizado del potencial ORP y pH en cada circuito.
Se debe tener cuidado con el uso de diésel oil en pulpas con alto contenido de gangas finas, pues induce arrastre físico de lamas y un gran aumento de la recuperación másica del circuito rougher.
No olvidar que la operación de la última etapa de limpieza columnar es clave, y opera mejor a un % de sólidos >20%. De su desempeño depende la ley de Mo del concentrado final (48-52%); y el contenido de insoluble (5-7%).
El uso de antiespumante P-4000 en canaletas y cajones debe hacerse con mesura, pues introduce un exceso de diésel oil al sistema, que en presencia de arcillas y otras gangas finas producirá problemas de espumación y aumento del arrastre físico de insoluble a los concentrados.
La recuperación de Mo en la planta de moly se favorece con el aumento de la ley de Mo en el concentrado colectivo Cu-Mo (entre 0.3 y 1.0%Mo). A su vez, las partículas de molibdenita flotan mejor si su tamaño está por sobre 10µm.